To contribute to the realization of a sustainable future, we are reinforcing collaboration between industry, academia, and government, including central government, local governments, and universities, to carry out various environmental preservation initiatives.
• Promote volunteer environmental protection activities
• Increase the capability to accommodate green ship recycling
• Participate in the collection and study of marine plastic pollution
We engage in various activities to raise the environmental consciousness of our employees further, including initiatives to protect biodiversity and create pleasing landscapes. We also are collaborating with the NPO Chiba University Students Committee for Environmental Management System to protect community nature areas and to clean up business sites and seashores.
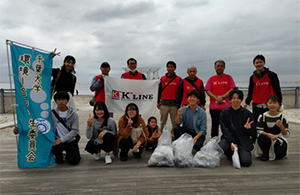
Various types of metal are used in ships.
The metals collected after dismantling ships are valuable resources and can be recycled into new products and used for new services to support local lives and the development of employment. The "K" LINE Group strives for responsible dismantling and recycling of resources also in the ship scrapping stage. When we dismantle ships, we inspect ship recycling yards and use our unique "K" LINE checklist to carry out environmental impact assessment to check whether the work is being carried out safely, whether substances that affect the human body or the environment are being properly collected, and whether the dismantling process has an impact on the surrounding environment and so on.
In 2009, the international Maritime Organization(IMO)has adopted the "Hong Kong International Convention for the Safe and Environmentally Sound Recycling of Ships, 2009"(HKC)for safe and environmentally friendly recycling of ships, and the ratification is proceeding toward its entry into force.
In anticipation of the early ratification, we are working on dismantling ships and recycling resources with due consideration to environmental protection and occupational safety and health.
In 2017, ”K” LINE established the company rules "Operating Rules for Ship Recycling" and "Detailed Operating Rules for Ship Recycling" to ensure that the dismantling work is carried out in consideration of environmental protection and occupational safety and health.
"The evaluation method for ship dismantling yards based on our own evaluation criteria"
Dismantling of vessels owned by our company requires to be conducted only at our certified yards selected according to our own evaluation criteria in consideration of the conformity requirements of the HKC and our own perspective in addition. The evaluation is conducted at on-site audit in cooperation with our local supervisors. The main yard evaluation criteria consist of the followings.
・Status of acquisition of the international standard certifications
(HKC Conformity Certificate (Ship Recycling Convention), ISO14001(Environmental Management), ISO45001(Occupational safety Management), ISO9001(Quality Management), etc.)
・Operation Procedures
・Various records(Ship Recycling Plan(SRP), Ship Recycling Facility Plan(SRFP), waste disposal record, etc.)
・Management's Recycling policy
・Organizational management system
・Pollution prevention measures
・Compliance with the Ship Recycling Plan
・Operation stats at the intertidal zone
・Management / maintenance status of yard facility, heavy machinery, other yard equipment, workers protective equipment, etc. used for dismantling
・Impermeability of the dismantling yard floor
・Compliance with no acceptance of child labors
・Health and safety measures
・Medical equipment
・Implementation of emergency drill and employee training
・Worker's insurance coverage
・Records of past accidents / Near miss report
”On-site reconfirmation of the certified yard before the ship docking-in”
Before dismantling a ship, we dispatch supervisors to the dismantling yard to reconfirm equipment and operational status of the yard or we reconfirm by ourselves.
”Monitoring system from the start of dismantling to the completion”(Conducting about 10 times on average)
During the dismantling, we dispatch a supervisor to the yard to monitor the dismantling work.
In the monitoring work, we mainly check the following items.
・Compliance status with Ship Recycling Plan
・Security management status near the gate-entrance
・Removal of dangerous materials
・Access control to restricted areas including dangerous space
・Destruction process of radio communication equipment
・Marking of materials containing asbestos
・Removal of oil
・Management and the actual working conditions for dangerous work such as gas cutting work, working aloft, working in enclosed space etc.
・Certificate of work completion by a public institution
"Regular yard audits to maintain the standard of the certified yard"
- 拡大
- Interview with the yard managers
We carry out regular on-site visits to our certified yards to confirm that they continue to meet our certification standards. In case an accident or violation occurs, we request the yard for status reports and countermeasures, and we take measures to exclude them from our green certification list until improvements are confirmed. We also exchange opinions with authorities, industry organizations, and other external related organizations to promote environmental protection and occupational safety and health for the entire industry, as well as industry policies and facilities inside and outside the yard such as TSDF:Treatment, Storage and Disposal Facility(final disposal site for waste.)We are monitoring the progress in the development.
- 拡大
- Ship recycling yard on work
Monitoring activities for dismantling work
- 拡大
- Ship recycling yard on work
The dismantling work takes a long time, but we ask our local supervisors to report regularly and monitor until it is completed.
- 拡大
- Ship recycling yard on work
Through measures such as use of iPads and paper-saving printer settings (double-sided printing and printing two pages per each side of paper), we are reducing our use of office paper. We also separate office waste into 12 different types and try to recycle it into resources whenever possible.
We employ a system for office purchases whereby priority is given to purchasing products that comply with the Act on Promoting Green Purchasing or are EcoMark-certified. We sum up the amount of expenses for purchasing goods and the ratio of green purchases each month and distribute the results widely throughout the Company in order to further increase consciousness about reducing costs and purchasing eco-friendly goods/products.
On September 1, 2015, our office started to collect PET bottle caps which had been disposed of as plastic garbage every day. The purpose of this activity is reducing CO_{2} emissions from the incineration of PET bottle caps; and making the activity a help for social contribution by donating the proceeds from sale of PET bottle caps to charity.
Results of this activity of handing over the PET bottle caps to Minato-ku Recycling business Cooperative in the past are as follows:
|
The massive amount of plastic waste flowing into the sea has become a worldwide issue.
In order to maintain the beautiful blue and fertile oceans, we participate in “Plastics Smart Forum” conducted by the Ministry of the Environment.
※Plastics Smart Forum
The Plastics Smart Forum is a platform set up to promote dialogue and interaction among companies and organizations concerned about marine plastic waste, by supporting the expansion and activation of each initiative so as to promote the “Plastics Smart ” approach nationwide toward the elimination of marine plastic waste.
Plastics Smart Website: http://plastics-smart.env.go.jp(Japanese text only)
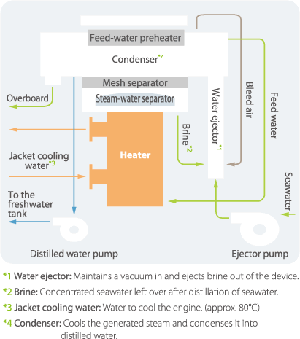
Most of the water used for daily living on ships is seawater that has been purified using 80°C jacket cooling water that was used to cool the engine during a voyage. The interior of the freshwater generator is maintained as a vacuum to lower the boiling point of the water so that seawater fed to the device is vaporized by the heat of the jacket cooling water. It is then condensed by the condenser to make distilled water that is used for various purposes on board.
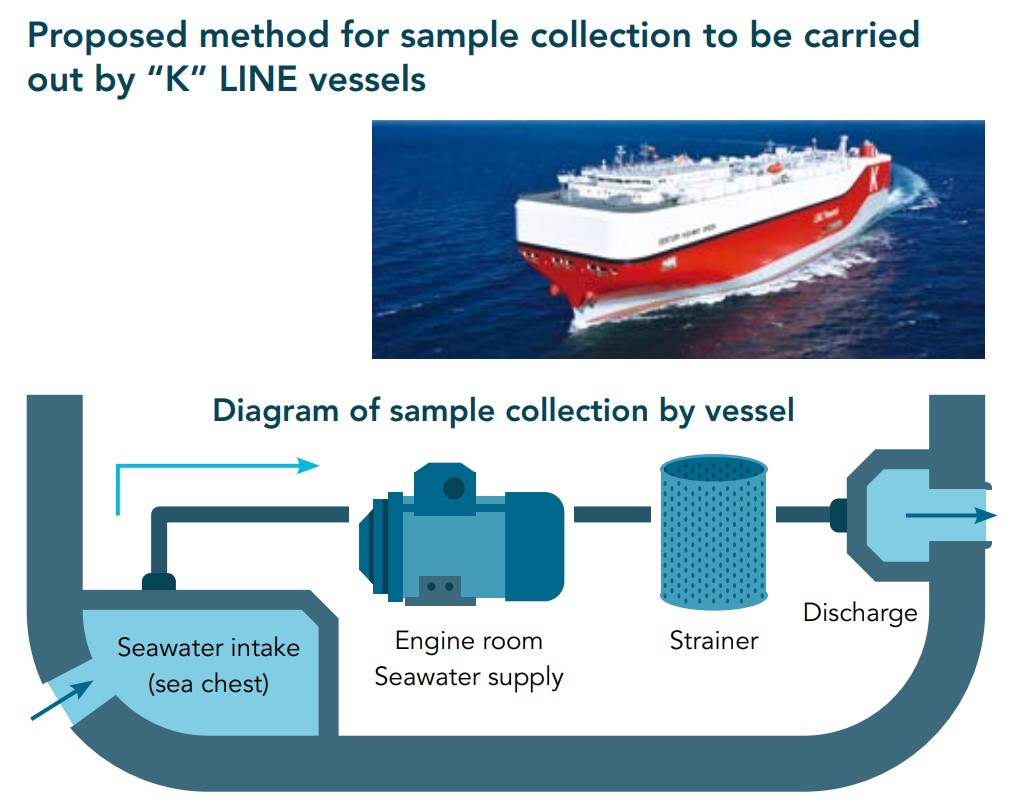
“K” LINE has signed an agreement with Tokyo University of Marine Science and Technology to start joint research on marine plastics. The joint research will evaluate how much plastic waste can be collected from common seawater intake that is filtered by ships on voyages. Specifically, “K” LINE vessels will take samples from the seawater intake line with a strainer while the ship is running, and then the university will collect plastic particles from the samples and analyze their material, size, and other properties. The aim for this project is that it will lead to further research, such as the collection of microplastics in the open sea using ocean- going vessels and the establishment of a system for monitoring the density of microplastics in specific areas.
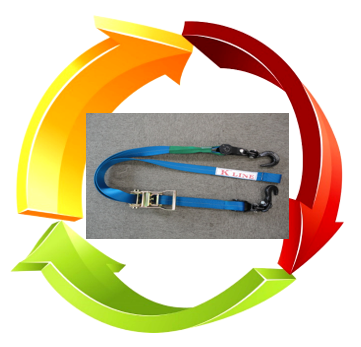
We have developed a scheme to recycle the used lashing belts that are used to secure vehicles on pure car carriers (PCCs).
The metal parts of the lashing belts are recycled as products, while the plastic parts are incinerated and used as raw materials for cement or melted down to create slabs and roadbed materials.
This initiative not only considers the natural environment but also supports the employment of people with disabilities by outsourcing the sorting of lashing materials to facilities that provide employment support.
In addition, for users of a workplace under Continuous Employment Support Type A (*1), the intermediate processing company actively creates employment opportunities within their organization and builds a system to provide continued support for their employment.
※For more details, please refer to the link below.
Relationship with the Community | Social | Sustainability | Kawasaki Kisen Kaisha, Ltd.
|
*1 A welfare service that allows people who have difficulty finding employment at general companies to work in the workplace through the conclusion of employment agreement, etc.
(kWh)